
Solution Story: Automation Integrator uses Pepperl+Fuchs Comtrol for Device ConnectivityĪ leading integrator of factory automation and robotics solutions selected the Pepperl+Fuchs Comtrol DeviceMaster UP 2-port 2E for a production line cell for forging spindles. As fracking helps to release natural substances (in this case, oil) from the earth’s rock for extraction, monitoring sensors directly at the site provide data and supervisory control for engineers and personnel controlling the fracking process. Solution Story: Hydraulic Fracking Process Monitoringįracking, otherwise known as hydraulic fracturing, has become a word well-known with the recent expansion of oil exploration. Siemens use: coils (generally addressed as 0xxxx), contacts (1xxxx), input registers (3xxxx), holding registers (4xxxx).DeviceMaster Industrial Gateway DIN Rail FamilyĭeviceMaster Industrial Gateway Panel Mount FamilyĭeviceMaster Industrial Gateway Rack Mount Family Some MODBUS units use designated addresses for each function code, i.e. Important info for Server applications with Siemens clients(masters) Use the script functions read_port_bit() and write_port_bit(, ) to read and write to those addresses on your robot from the running program. Use function codes 0x01: READ_COILS, 0x02: READ_DISCRETE_INPUTS, 0x05: WRITE_SINGLE_COIL, 0x0F: WRITE_MULTIPLE_COILS to access the following addresses. Please note that some registers has been added and the list below has been marked what registers is avalable from what version. Use the script functions read_port_register() and write_port_register(, ) to read and write to those addresses on your robot from the running program. Use function codes 0x03: READ_HOLDING_REGISTERS, 0x04: READ_INPUT_REGISTERS, 0x06: WRITE_SINGLE_REGISTER, and 0x10: WRITE_MULTIPLE_REGISTERS to access the following addresses. Setup the controller IP and your MODBUS client with static IP addresses in the same subnet, see Modbus TCP client set up address 3 on the robot will be address 4 on the Anybus X-gateway) Anybus X-gateways), then just add one to the address on that device. Be aware that some other devices are 1-based (e.g. The MODBUS Server has 0-based addressing. Note that all values are unsigned, if you want to convert to signed integers, program "if (val > 32768): val = val - 65535". Coils (digital ports) can be accessed using read_port_bit() and write_port_bit(,). You can use the script function integer_to_binary_list() to get the register value as a list of booleans (e.g.), or binary_list_to_integer() to go back, please refer to the URScript manual for details. The 16 bit ports can be read using the script function read_port_register(), many of the ports, including 128 general purpose registers (address 128-256) (see the port map) can also be written to using write_port_register(,).

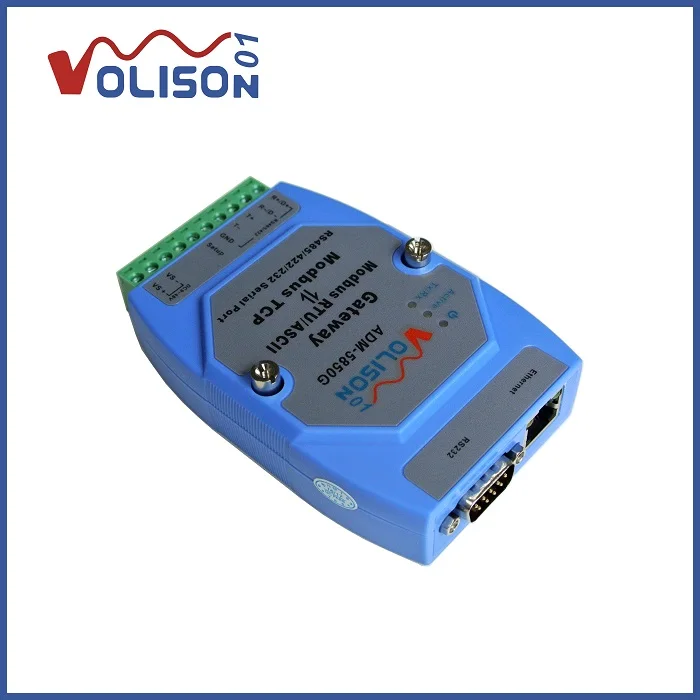
Some Modbus device manufacturers use the terms Master (client) and Slave (server).

The server is available at the IP address of the controller which can be found and modified in PolyScope (SETUP Robot → Setup NETWORK) For more information about MODBUS, see of MODBUS messages can be found at The robot controller acts as a Modbus TCP server (port 502), clients can establish connections to it and send standard MODBUS requests to it.

Give read and write access to data in the robot controller for other devices Note that older or newer software versions may behave differently.
